Renault Industria Mecánica Tecnología
¿Cómo lo lograron? La historia de éxito de la planta de Renault en Valladolid
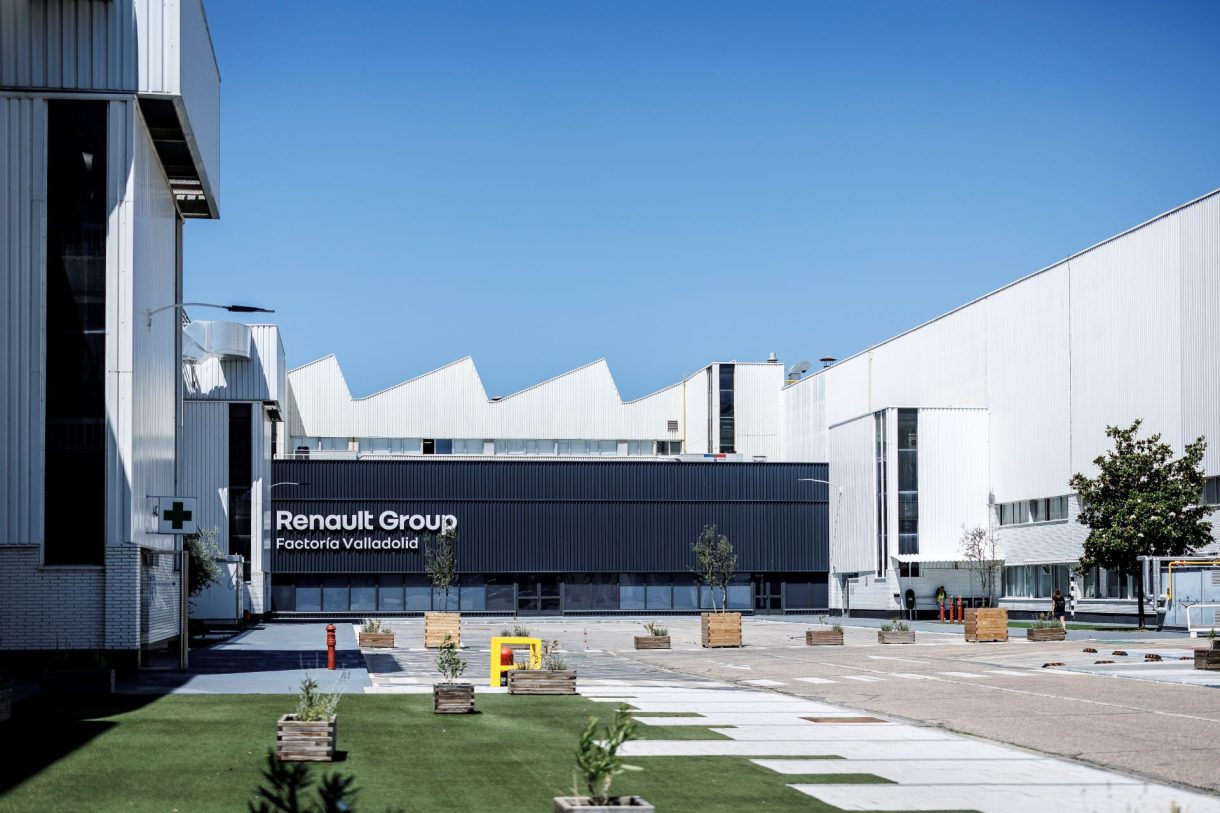
La fábrica de Renault en Valladolid, inaugurada en 1972, ha recorrido un largo camino de evolución y mejora. Con más de 8 millones de vehículos fabricados y múltiples premios en calidad, medio ambiente y prevención de riesgos laborales, esta planta se ha consolidado como un referente en la industria automotriz. Hoy en día, cuenta con […]
La fábrica de Renault en Valladolid, inaugurada en 1972, ha recorrido un largo camino de evolución y mejora. Con más de 8 millones de vehículos fabricados y múltiples premios en calidad, medio ambiente y prevención de riesgos laborales, esta planta se ha consolidado como un referente en la industria automotriz. Hoy en día, cuenta con 2259 trabajadores, de los cuales un 27% son mujeres, y mantiene un ritmo de producción que involucra a 900 empleados por día en dos turnos.
Uno de los aspectos más destacados de la planta de Valladolid es su enfoque y preocupación en garantizar la máxima calidad en todos sus procesos de fabricación. La llegada de nuevos modelos ha intensificado los controles de calidad, asegurando que cada vehículo que sale de la línea de montaje cumpla con los más altos estándares. Este compromiso con la excelencia ha permitido que hasta el 90% de la producción se exporte a otros países, una prueba del reconocimiento global de la calidad de Renault.
Actualmente, la planta fabrica desde cero los modelos Captur en sus versiones gasolina, HEV y GLP, el Symbioz en versión HEV, y el Mitsubishi ASX también en versiones gasolina, HEV y GLP. Este es un hito significativo, ya que es la primera vez que la fábrica de Valladolid produce un segmento C, similar a lo que sucede en la planta de Palencia con el Rafale, su primer segmento D. La producción ha aumentado un 18%, lo que subraya y destaca la capacidad de adaptación y crecimiento de la planta a unos niveles increíbles.
Renault ha apostado por la innovación y la digitalización, convirtiendo su planta de Valladolid en una fábrica piloto que se sitúa a la vanguardia de la industria consiguiendo la máxima eficiencia tanto energética como de rentabilidad. La integración de robots y tecnología avanzada ha permitido una automatización casi completa, especialmente en el proceso de chapa, donde se han automatizado el 99% de los robots. Esta sección, que emplea a 350 trabajadores, se especializa en la fabricación de componentes plásticos y es la más grande de Renault en el mundo.
La marca francesa ha implementado un enfoque integral de descarbonización, desde la cadena de suministro hasta la producción y el reciclaje. En Sevilla, por ejemplo, se da una segunda vida a los vehículos usados, mientras que en Valladolid se ha logrado una reducción del 42% en el consumo de energía y del 39% en el consumo de agua. Este compromiso con la sostenibilidad ha sido reconocido con premios a la sostenibilidad y ha posicionado a Renault como un líder en la industria gracias a una investigación constante en todos sus procesos de fabricación:
1.Proceso de chapa
2.Producción de baterías
La planta de Valladolid también se destaca por su taller de baterías, donde se ensamblan tres tipos distintos de baterías híbridas y enchufables. La producción anual es de 300.000 baterías, con una capacidad de 60 baterías por hora y una automatización del 40% del proceso. En el caso de las baterías PHEV, la producción anual es de 30.000 unidades, con una capacidad de 10 baterías por hora y una automatización del 15%.
Para la versión PHEV del Rafale, Renault contará con baterías de BYD, que ofrecen una autonomía de 80 km y una capacidad de 22 kWh. Estas baterías son sometidas a rigurosos tests mediante inteligencia artificial para garantizar la máxima calidad y eficiencia.
3.Proceso de pintura
El departamento de pintura de la planta cuenta con 92 robots que han permitido automatizar procesos críticos, como la eliminación de hornos, reduciendo el número de cuatro a uno. Gracias a la técnica 4wet, se ha logrado un ahorro del 40% en el consumo de gas y del 10% en el consumo de electricidad. Este proceso no solo es eficiente, sino que también asegura un alto nivel de calidad, ofreciendo siete colores de carrocería y tres opciones bitono.
4.Montaje y control de calidad
La línea de montaje es la más grande de la planta, con 1121 trabajadores repartidos en dos equipos diarios que permiten ensamblar un vehículo en menos de un minuto. Aquí se producen motores de gasolina, GLP, microhíbridos y híbridos eléctricos (HEV). Cada vehículo es sometido a una serie de pruebas rigurosas para garantizar su calidad, incluyendo pruebas de velocidad, frenos, suspensión, luces o incluso los sistemas ADAS.
Renault no se detiene aquí. La próxima motorización del Rafale contará con una versión e-tech full hybrid 4×4 de 300 CV, con una autonomía eléctrica de 100 km y un consumo reducido a 0.7 litros a los 100 km. Además, la planta ha generado 500 nuevos empleos y se espera que cumplan su promesa de crecimiento y sostenibilidad en los próximos años.
Deja un comentario